您是否遇到過造粒機產量不穩定或顆粒不均的問題? 在塑料、化工、食品加工等領域,擠出機與造粒機的協同作業是生產流程中的核心環節。一套規范的操作流程不僅能提升設備效率、降低能耗,更是保障產品質量的關鍵。本文將系統拆解擠出機操作流程造粒機的核心步驟,幫助操作人員規避常見誤區,實現高效生產。
一、操作前準備:設備調試與原料處理的科學法則
“七分準備,三分操作”是工業設備運行的黃金準則。在啟動擠出機前,需完成以下關鍵步驟:
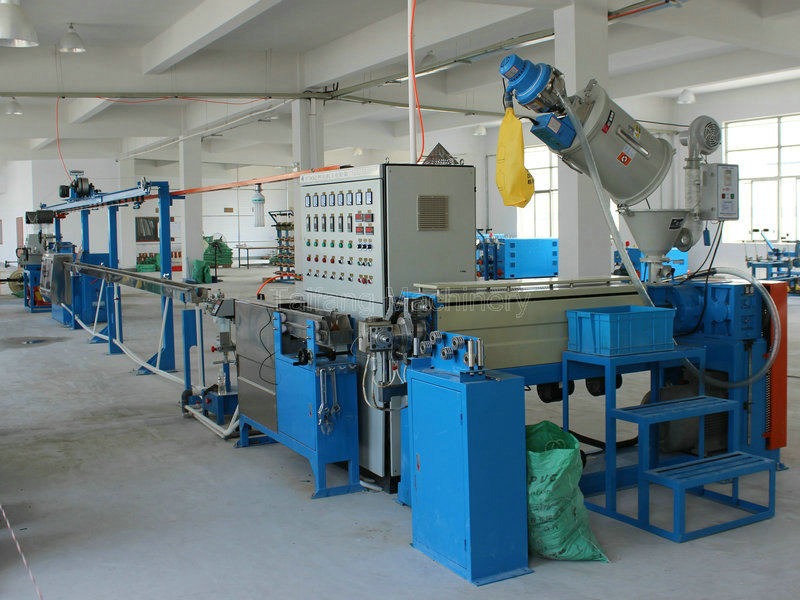
- 設備狀態檢查:確認螺桿、機筒無殘留物或銹蝕,加熱圈、溫控儀表工作正常,冷卻水循環系統無泄漏。
- 溫度參數設定:根據原料特性(如PP、PE或生物降解材料)設定五段加熱區溫度,通常遵循“前低后高”原則,避免熔體過早塑化導致螺桿扭矩異常。
- 原料預處理:含水量超標的物料需進行真空干燥(建議濕度≤0.03%),防止擠出過程中產生氣泡或降解反應。
二、開機運行流程:溫度控制與壓力監測的平衡藝術
第一階段:階梯式升溫
采用分階段加熱策略:
- 先預熱至150℃(以PE為例),保溫20分鐘使熱傳導均勻
- 每15分鐘升溫30℃,最終達到工藝溫度(通常190-230℃)
此過程可有效減少熱應力集中,延長螺桿使用壽命。
第二階段:低速喂料啟動
- 啟動主電機時,螺桿轉速控制在10-15r/min
- 觀察電流表波動范圍(正常值應為額定電流的60-70%)
- 當模頭出料呈現連續均勻條狀時,逐步提速至設計產能的80%
第三階段:造粒機協同調控
- 調整切刀轉速與擠出速度的速比關系(推薦1:1.2-1.5)
- 通過*風冷系統*控制顆粒結晶度,水溫建議保持在25-35℃
- 使用激光粒度儀抽檢顆粒直徑,偏差應≤±0.3mm
三、工藝參數優化:提升產能與質量的實戰技巧
1. 螺桿組合設計
針對不同物料特性選擇螺桿結構:
- 漸變型螺桿:適合熱敏性材料(如PVC)
- 突變型螺桿:適用于結晶性塑料(如PA66)
- 混煉段增加銷釘或屏障結構,可提升分散性23%以上
2. 熔體壓力精準控制
- 安裝熔體壓力傳感器(建議范圍15-25MPa)
- 通過*變頻喂料機*調節下料速度,壓力波動需≤±1.5MPa
- 典型案例:當壓力超過28MPa時,需立即檢查濾網堵塞情況
3. 能耗比優化方案
- 采用電磁感應加熱替代電阻加熱,節能率可達30-40%
- 建立溫度-轉速-壓力的三維控制模型,實現動態能耗管理
四、停機維護要點:延長設備壽命的關鍵操作
規范停機程序直接影響設備可靠性:
- 生產結束前30分鐘:逐步降低喂料量至50%
- 切換清洗料:使用專用螺桿清洗劑或低粘度樹脂(如HDPE)
- 降溫流程:
- 先關閉加熱電源,保持螺桿低速運轉
- 當機頭溫度降至80℃以下時停轉螺桿
- 嚴禁急冷急熱,防止零部件變形
周期性維護計劃:
- 每500小時檢查螺桿磨損量(允許公差≤0.08mm)
- 每月清洗液壓油濾芯,年度更換齒輪箱潤滑油
- 建立振動監測系統,預警軸承故障前兆
五、質量控制體系:從過程參數到成品檢測的全鏈路管理
構建SPC(統計過程控制)體系是確保穩定輸出的核心:
- 在線監測指標:
- 熔體流動速率(MFR)波動范圍≤±5%
- 顆粒外觀合格率≥99.2%(通過CCD視覺檢測)
- 實驗室檢測項目:
- 灰分含量(執行GB/T 9345標準)
- 拉伸強度(ASTM D638)
- 熔融指數偏差(每2小時抽檢)
- 異常處理機制:
- 建立*顏色管理看板*實時反饋質量狀態
- 制定顆粒結塊、黑點等問題的8D分析流程
通過上述系統化的操作規范,企業可將造粒機綜合效率(OEE)提升至85%以上,同時降低噸能耗成本18-25%。值得注意的是,操作人員的經驗積累與設備智能化升級的有機結合,才是實現高效穩定生產的終極解決方案。
TAG: