你知道嗎?全球每年消耗的聚丙烯(PP)材料超過6000萬噸,從食品包裝到汽車零部件,這種輕質、耐腐蝕的塑料幾乎無處不在。然而,如何將顆粒狀的PP原料轉化為高精度、高性能的終端產品?答案藏在PP擠出機生產線的智能化設計與精密工藝中。本文將深入解析這一生產系統的核心技術與行業應用,揭示其在現代制造業中的關鍵作用。
一、PP材料特性與市場需求驅動生產線革新
聚丙烯(PP)因其耐高溫、抗沖擊、易加工的特性,成為塑料工業的“黃金材料”。隨著環保政策趨嚴和消費升級,市場對PP制品的需求呈現兩大趨勢:
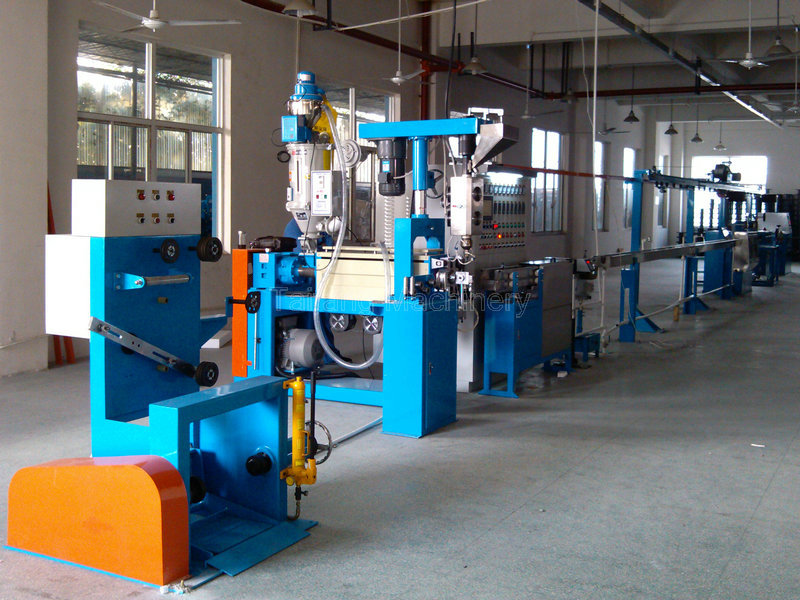
- 定制化:汽車輕量化要求PP配件具備更高強度;
- 綠色化:可回收PP包裝材料替代傳統塑料已成主流。
為滿足這些需求,PP擠出機生產線通過模塊化設計實現靈活適配,例如通過更換模具,同一設備可生產管材、板材、片材等多種產品,生產效率提升30%以上。
二、PP擠出機生產線的核心構成與技術突破
一條完整的PP擠出機生產線通常包含原料處理系統、擠出主機、成型模具、冷卻定型、牽引切割五大模塊。其中,三大技術革新正在重塑行業標準:
- 雙螺桿擠出機的智能化升級
傳統單螺桿設備易出現塑化不均問題,而*雙螺桿擠出機*通過嚙合式螺桿設計,實現原料混合均勻性與溫控精度的雙重提升。搭載物聯網傳感器后,設備可實時監測壓力、溫度參數,自動調節轉速,能耗降低15%-20%。
- 多層共擠技術的突破
在食品包裝領域,PP材料需與EVOH阻隔層復合使用。通過多層共擠模頭,生產線可一次性完成3-5層材料的同步擠出,既保障阻氧性能,又避免分層風險。
- 在線質量檢測系統
采用激光測徑儀與紅外熱成像儀,生產線能在0.1秒內識別厚度偏差或溫度異常,廢品率從5%降至1%以下。某知名汽車配件廠商引入該系統后,年節省原料成本超200萬元。
三、行業應用場景與效益分析
PP擠出機生產線的泛用性使其在多個領域大放異彩:
- 汽車工業:生產保險杠、內飾板等輕量化部件,較金屬件減重40%;
- 包裝行業:制造可微波加熱的PP餐盒,耐溫達120℃;
- 建筑領域:擠出PPR管道,抗壓強度達20MPa,使用壽命超50年。
以某家電企業為例,其采用新型擠出生產線后,PP洗衣機內筒的日產能從500件提升至1200件,產品合格率穩定在98.5%以上。
四、選購PP擠出機生產線的四大黃金法則
面對市場上琳瑯滿目的設備,如何選擇高性價比的解決方案?
- 匹配產能需求:根據目標產量選擇螺桿直徑(常見45-120mm)與驅動功率;
- 關注能耗指標:優先選擇配備伺服電機與熱回收系統的機型;
- 驗證廠家資質:考察是否具備CE認證或ISO9001質量管理體系;
- 售后支持能力:確保提供模具開發、工藝調試等一站式服務。
五、未來趨勢:綠色制造與智能化深度融合
隨著工業4.0推進,PP擠出機生產線正朝著兩個方向進化:
- 數字孿生技術:通過虛擬仿真預判設備故障,減少停機損失;
- 生物基PP加工:適配可再生PP原料,碳排放降低30%。
據《全球塑料機械市場報告》預測,到2028年,智能擠出設備的市場份額將突破70%,成為行業主流選擇。
從原料到成品,PP擠出機生產線不僅是技術的集成,更是效率與品質的保障。無論是初創企業還是行業巨頭,只有掌握核心工藝邏輯,才能在這場“塑料革命”中搶占先機。
TAG: