在塑料加工領域,PVC擠出機的高效運行直接決定了產品質量與生產效率。然而,許多操作人員在實際生產中常因參數設置不當,導致產品出現表面粗糙、尺寸偏差甚至設備損壞等問題。掌握溫度、螺桿轉速、壓力等核心參數的調節(jié)技巧,不僅能提升成品率,更能延長設備壽命——這正是每位工程師必須精通的”基本功”。
一、溫度控制:擠出工藝的”生命線”
PVC材料的加工特性決定了溫度敏感性。擠出機通常分為進料段、壓縮段、熔融段和均化段,每個區(qū)域的溫度設定需遵循”梯度升溫”原則:
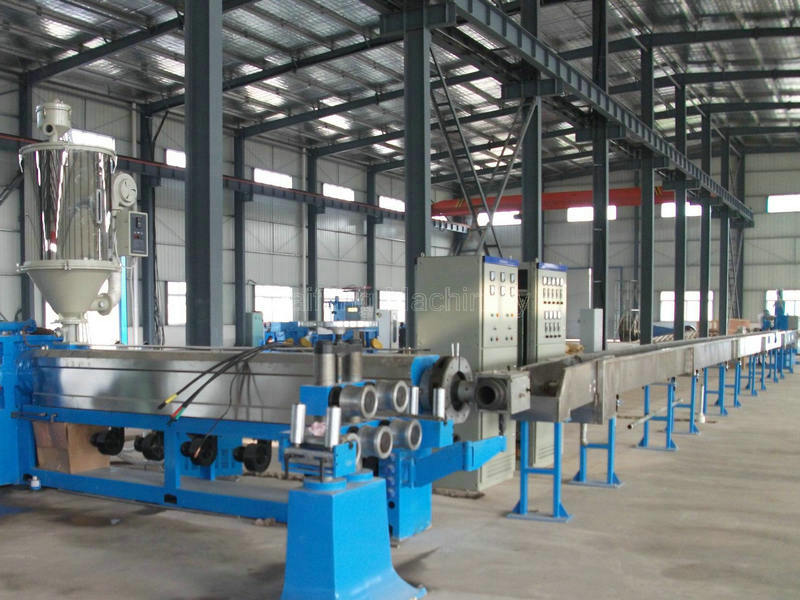
- 進料段(160-170℃):溫度過高會導致原料過早塑化堵塞進料口,溫度過低則影響輸送效率
- 熔融段(180-190℃):此階段需完全熔融PVC顆粒,溫度波動超過±3℃即可能引發(fā)分解反應
- 模頭段(175-185℃):適當降溫可穩(wěn)定產品定型,但需與冷卻系統形成協同效應
典型案例:某管材生產企業(yè)通過將均化段溫度從195℃降至185℃,成功將氣泡缺陷率從12%降至1.8%。
二、螺桿轉速:速度與質量的平衡藝術
作為擠出機的心臟部件,螺桿轉速直接影響產量與塑化效果。調節(jié)時需注意:
- 轉速與溫度聯動:每提升10rpm,熔體溫度可能上升2-3℃,需同步調整加熱系統
- 背壓控制:保持0.5-2MPa背壓可提高塑化均勻性,但超過3MPa會加速螺桿磨損
- 產量公式:Q=πD2hN/4(D螺桿直徑,h螺槽深度,N轉速)可作為理論參考值
黃金法則:對于φ65mm螺桿,生產3mm壁厚管材時,建議轉速控制在25-35rpm區(qū)間。
三、模具壓力:決定產品精度的”無形之手”
模頭壓力調節(jié)常被忽視,卻是影響產品尺寸穩(wěn)定性的關鍵因素:
- 壓力監(jiān)測:安裝熔體壓力傳感器(建議量程0-40MPa)
- 調節(jié)技巧:
- 通過口模平直段長度調整:每增加10mm長度,壓力提升約15%
- 采用阻流塊微調:可改變局部熔體流速分布
- 預成型板優(yōu)化:將開孔率控制在60-70%可平衡壓力與流速
某型材生產企業(yè)通過優(yōu)化模具壓縮比(從3:1調整為2.5:1),使角線接縫問題減少70%。
四、冷卻系統:容易被低估的關鍵環(huán)節(jié)
冷卻效率直接影響產品結晶度和機械性能:
- 真空定徑箱水溫建議控制在12-18℃,溫差需穩(wěn)定在±1℃以內
- 噴淋冷卻角度應調整為45°入射,確保管材周向均勻冷卻
- 牽引速度匹配公式:V=Q/(ρ×A)(Q擠出量,ρ材料密度,A截面積)
注意:過快的冷卻會導致內應力積聚,建議采用”梯度降溫”法,第一段冷卻水溫比后續(xù)段高5-8℃。
五、參數聯動:系統化調整策略
擠出工藝本質是多參數耦合系統,建議建立以下調整流程:
- 根據配方確定基礎溫度曲線
- 以60%額定轉速啟動設備
- 觀察熔體壓力波動是否在±5%范圍內
- 通過在線測徑儀實時反饋調整牽引速度
- 每調整一個參數后,需穩(wěn)定運行15分鐘再記錄數據
某薄膜生產企業(yè)通過引入MES系統,將參數調整時間從3小時縮短至45分鐘,廢品率降低40%。
六、常見問題快速診斷表
現象 |
可能原因 |
解決方案 |
表面鯊魚皮 |
熔體溫度過低 |
提升模頭段溫度3-5℃ |
軸向條紋 |
螺桿轉速過高 |
降低10-15rpm并檢查濾網 |
截面橢圓 |
冷卻不均勻 |
校準真空箱水位與噴淋角度 |
顏色發(fā)黃 |
局部過熱分解 |
檢查加熱圈接觸與熱電偶精度 |
掌握這些核心參數的調節(jié)邏輯,就能讓PVC擠出機從”能用”變?yōu)?rdquo;好用”。隨著智能控制技術的普及,參數優(yōu)化正從經驗驅動轉向數據驅動,但基礎原理的深刻理解始終是技術升級的基石。
TAG: